MAPLAN SPECIAL⁺ QUATTRO-RAM: FOURFOLD POWER FOR E-MOBILITY
E-cars are demanding new solutions, in rubber processing as well. The new MAPLAN SPECIAL+ QUATTRO- RAM 700-700/850 injection moulding machine was specially designed for the production of battery seals in the electric car industry. It is the largest machine to have left the MAPLAN production hall in Austria to date.
With a unit weight of approximately 100 tonnes and dimensions of around 8 x 9 x 6 m, this injection moulding monster broke all of MAPLAN’s previous records and demanded maximum performance from both the MAPLAN construction team and the transporters.
BIG & FAST:
CLOSING UNIT AND HEATING PLATES
IN IMPRESSIVE DIMENSIONS
Eight tie bars each with a diameter of 170mm ensure the mechanical stability of the locking unit. The four impressive main locking cylinders guarantee perfect locking force distribution across the 1500 x 2500mm size of the heating plates. Just two 50 kW pumps with a hydraulic pressure of 260 bar are required to ensure that movements are fast and smooth despite its size and enormous weight.
The servo-electrically driven MAPLAN Fast Double Shuttle moves two alternating centre plates and guarantees that continuous unloading or loading is pos-sible during the heating time. The travel speed in this process is a remarkable 600mm per second. The long travel distance of 3200mm is covered in just seven seconds.
The generously dimensioned and movable heating plates use automatic contacting for the heating cur-rent in the particular end position of the shuttle and in the machine. This keeps the temperature of the al-most permanently heated lower part of the mould stable. The software-controlled, hydraulic auto-levelling system for the ejectors compensates for the dynamic load during shuttle movement.
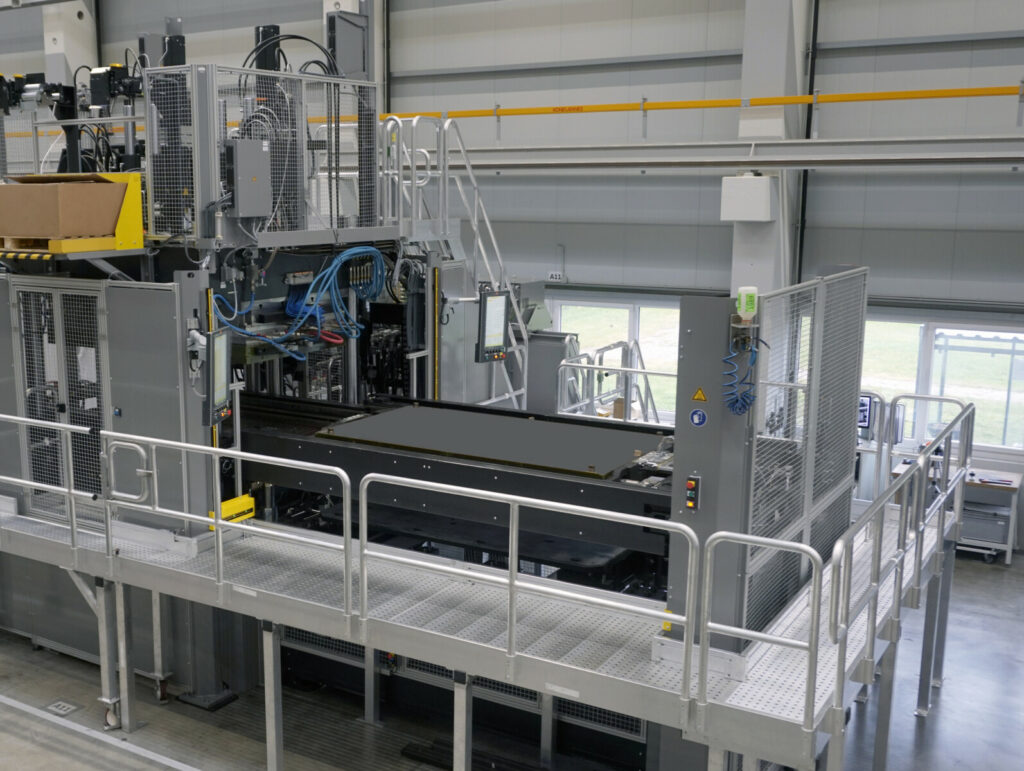
2K: WITH RUBBER & SILICONE
The injection system with two 700 ccm MAP.fifo injection units and independent hydraulics also had to be adapted to the new size. Special injection chambers designed for the powerful injection plates of the 850-tonne machine are used. Both rubber and silicone (multi-compound) can be processed with the two injection units (multi-component).
During silicone processing, the material is fed into each injection unit via a vertically arranged 15 litre stuffing unit. For rubber processing, all that needs to be remo-ved is a sealing plug on the injection units. Despite the exceptional machine height, it is kept ergonomic by way of integrated climbing aids for the operator.

QUATTRO-RAM 560 with 4 clamping cylinders and two 700 ccm MAP.fifo injection units injected from the top.
KEY FACT:
20 TONNES
ONLY BASE PLATE WEIGHS
ONE component of the SPECIAL+ QUATTRO-RAM 700-700/850 is heavier than the total weight of most other injection moulding machines. Its surface area is about three times larger than the single largest machine built by MAPLAN to date. The mould weight is about four times heavier than a standard mould on a 460-tonne machine. In the picture below, you can see the machine’s moving plate.
To sum up in other words:
The SPECIAL+ QUATTRO-RAM is a machine of superlatives!
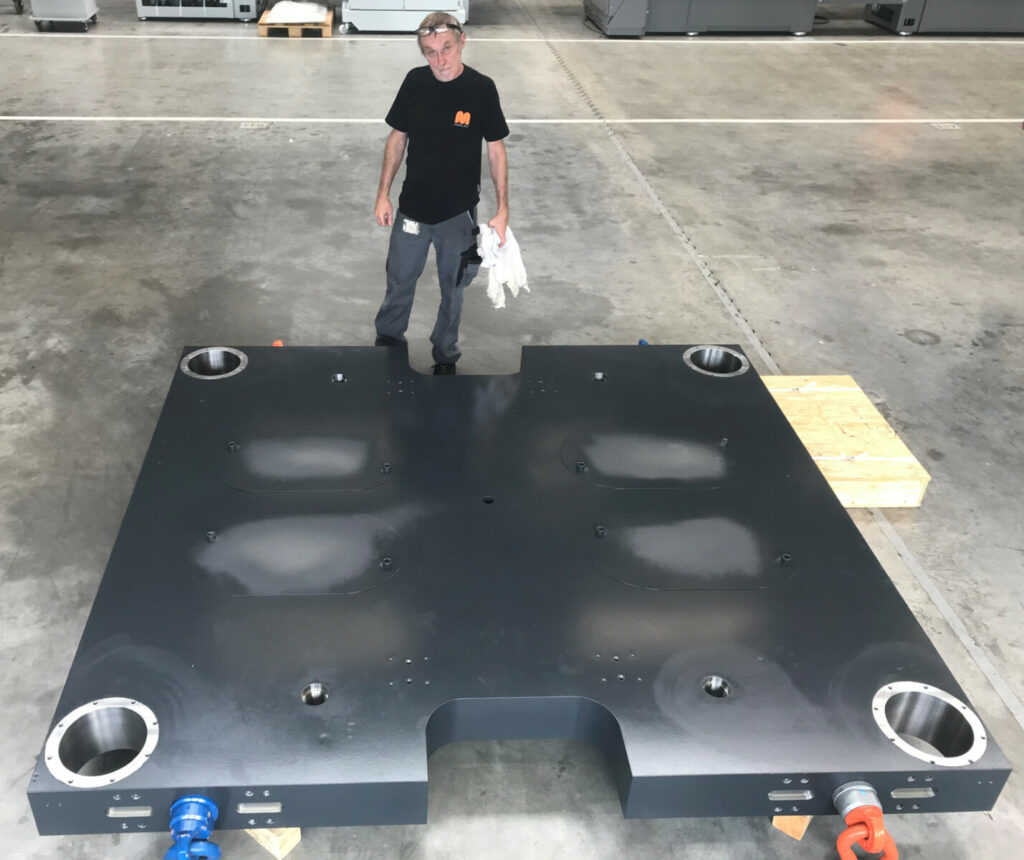