Rubber injection moulding can be so simple
New developments with respect to INJECTION INTELLIGENCE are focused on innovations that MAKE LIFE EASY for our customers. Just like most companies in the sector, MAPLAN was also affected by the corona crisis in recent months. However, development activities continued unabated for the most part. Free capacities were utilized for new developments in order to alleviate the daily lives of our customers.
HIGHER EFFICIENCY
BY MEANS OF TARGETED DYNAMIC PRESSURE ALLOCATION
Our new software version enables plasticizing process defined in 5-steps with individual speed and pressure settings. Shear energy input to the rubber compound can now be done with much more accuracy and efficiency and thereby reduces the fluctuation range of the temperature progression within the plasticizing procedure. This results in a significantly greater process window whereby the parts quality is more consistent and vulcanization or cycle times are significantly reduced.
HIGHER PROCESS TRANSPARENCY
ENSURES THE QUALITY OF PARTS
Process data is clearly consolidated and visualized for all MAP.fifo injection units. Pressure and temperature progression of the plasticizing process is depicted in an easily comprehensible manner according to cycles on three screen pages of the machine control system. The pages show configuration parameters including a process graph (Fig. 1), hydraulic pressure at the hydraulic motor and the temperature progression graph. The second illustration (Fig. 2) displays the pressure progression during plasticizing via which a tolerance range can be established for process monitoring. The quality of parts can be improved with this simple tool. Moreover, curve progressions can also be exported and added to parts-related data quality documentation.
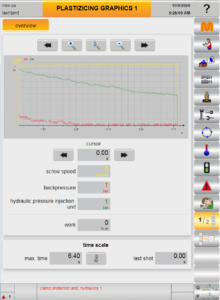
Fig 1. Overview page “Plasticizing” with graphic display of process parameters.
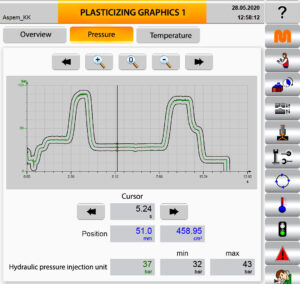
Fig 2. Pressure progression with generated envelope curve for tolerance monitoring.
MAP.COMPENSATE:
HEATING TIME MANAGEMENT
TARGETED, SIMPLE, EFFECTIVE
Various manufacturers have provided heating time calculation or process optimization systems for many years. However, most machine operators are overwhelmed by the multitude of material and machine parameters that must be entered in daily operations, which is why its usage has remained quite limited. MAPLAN is now introducing its own system in the form of MAP.compensate, which was developed with a focus on practicality. Up to 10 vulcanization times can be determined in advance per processed rubber mixture for various tool temperatures that are subsequently taken over in MAP.compensate. The control system uses this data to calculate the specific correlation between heating time and tool temperature. MAP.compensate returns the vulcanization process to the desired operating point by means of a calculated time correction if a deviation occurs in regard to this setting, e.g. due to an environmental drop in temperature. MAP.compensate determines a trajectory based on up to 10 mixture-specific and temperature-dependent heating times. These form the ideal basis for targeted heating corrections of environmentaloperating point deviations.
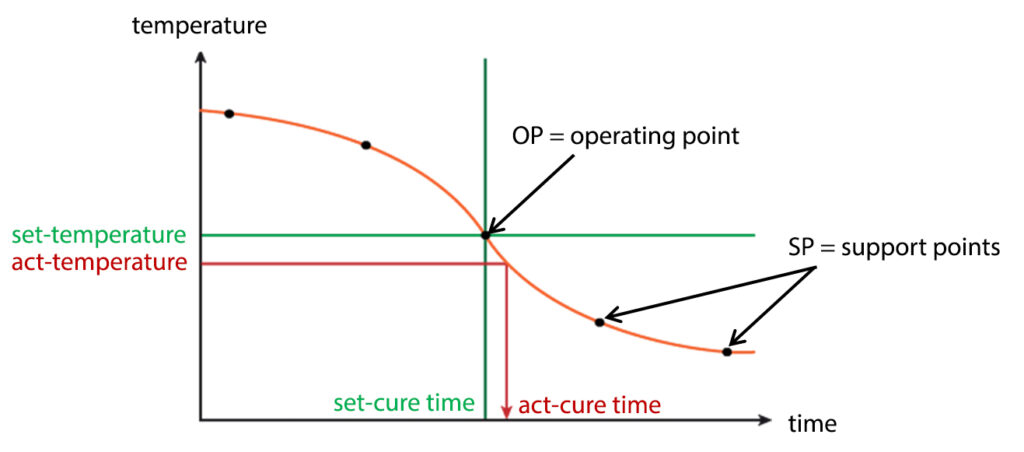
Fig. 3 MAP.compensate determines a trajectory based on up to 10 mixture-specific and temperature-dependent heating times. These form the ideal basis for targeted heating corrections of environmental operating point deviations.