Over two decades of manufacturing success through teamwork and technology
Mexico provides a low-cost supply base for many manufacturers in North America and around the world. Among others, the automotive industry has long enjoyed the cost advantages of sourcing from Baja California – the northern-most state in Mexico, just across the border from San Diego. But lowering costs isn’t everything, and in the wake of the global supply chain disruptions of 2020, purchasing directors are even more sensitive to one critical element: stability.
By partnering with Morgan Polymer Seals (MPS), automotive OEMs benefit from a reliable supplier that is privately-owned, debt-free, and experienced. And like MAPLAN, Morgan Polymer is a family company that provides personal customer service for its global partners. However, it is not easy to meet the demands of heavily-regulated car makers, so auto suppliers must deliver goods that adhere to strict quality standards. Starting with a single MAPLAN press in 1997, founder and CEO Kevin Morgan has quietly built a reputation as the innovative, on-time leader in precision rubber molding. Now, over two decades later, MPS continues to partner with MAPLAN for its Injection Molding, with seventeen machines that have helped the company earn distinguished quality awards from OEMs like Ford and General Motors, for several consecutive years.
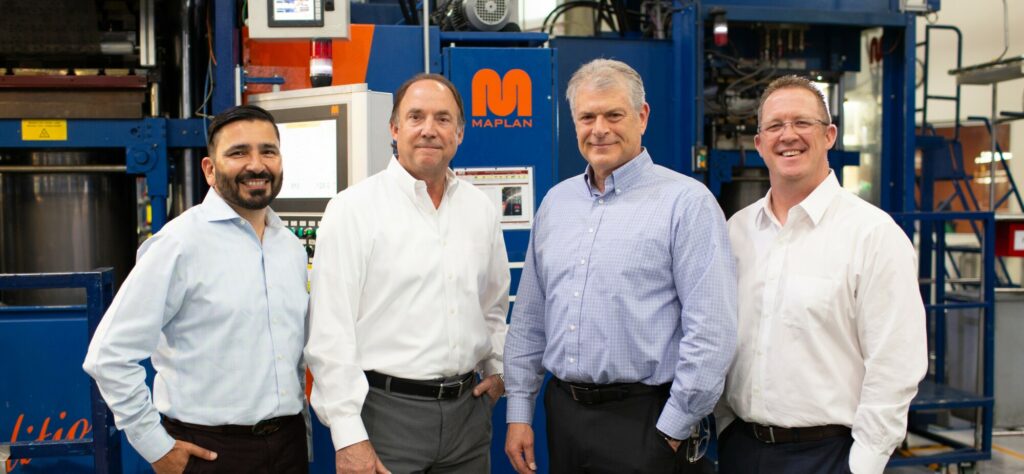
(Left to right) Alex Borboa, General Manager, Kevin Morgan, President & CEO, Mark Conlee, Director of Engineering, Todd Tesky, VP of Sales
ON-TIME DELIVERY WITH CUTTING-EDGE INJECTION MOLDING TECHNOLOGY
MPS has benefited from three generations of MAPLAN presses. “We’ve partnered with MAPLAN for our vertical-style injection molding presses since we started production. Their world-class machines help us achieve an industry-leading low scrap rate, which saves material,” says Alex Borboa, General Manager. MAPLAN has helped us increase our capacity, improve quality, and reduce costs.” Executives also highlight the machines’ long lifespan and range of refurbishing options. “The MAPLAN presses utilize a ‘full-stroking ram’ to evenly distribute the clamp tonnage over the entire surface of the mold, which helps to maximize the life of the tool and protect the customers’ tooling investment,” confirms CEO Kevin Morgan.
“For our company, MAPLAN presses are the best in the world”
Kevin Morgan, Founder and CEO
To support its promise of on-time delivery, MPS commits to the continuous improvement of its strict internal quality controls. Engineering Director Mark Conlee explains, “On-time delivery is the natural result of quality manufacturing. MAPLAN machines employ a FIFO (first in, first out) injection process to ensure only fresh rubber is injected in the mold. The result is high-quality, flawless articles without any cured residual material. At the same time, the vacuum technology helps eliminate air traps from the finished product. And with the vertical presses, we can maximize our capacity by operating two presses in the same space that it takes to run a single horizontal press. These benefits save cost and matches our processes perfectly. And when we save money, our clients save money.” And its dedication to the customer goes far beyond reducing costs. Morgan Polymer’s full-service logistics includes ’safety stock’ agreements, so customers enjoy peace of mind during seasons of unpredictable demand.
THE HARMONY OF GREAT PEOPLE WORKING WITH THE RIGHT TECHNOLOGY
CEO Kevin Morgan affirms, “There’s a right way to make every part – and it takes lots of experience to manufacture quality rubber seals.” Thus, it’s no surprise that Morgan Polymer Seals values enthusiasm, further training and positivity in its workforce. “We take care of the good people we’ve got. Good people want to be part of a winning team, so we track achievements and reward superior performance. From management to maintenance, everyone is essential and deserve an individual development program.”, says Sandra Martínez, HR manager. With centuries of combined engineering experience, Morgan Polymer’s engineers keep up with the latest advancements in precision rubber molding, robotics, and vision inspection. “MAPLAN always fully supports our new ideas for an even better production process”, adds Conlee. With the smart MAP.commander C6 control unit, MAPLAN supports every new production process introduced by its engineers. Furthermore, the userfriendly interface makes sure the machines are easy to operate.
A COMMON PHILOSOPHY BEST PRACTICE FOR THE FUTURE
MPS and MAPLAN share a common philosophy: continuous improvement. And the basis for this philosophy is a culture of discipline to support today’s goals and pave the way for a better future. Morgan Polymer’s Chief Revenue Officer, Sean Morgan, lays out the company’s plans: “Our future sees us expanding into new product segments, new markets, and exploring other exciting opportunities. These are uncertain times for many mid-sized companies, but we’re fortunate to be thriving from a strong financial position and experienced leadership. We’re excited to see what the future holds.”
Morgan Polymer Seals is a full-service, precision rubber molding company based in Baja California. To learn more, visit www.morganpolymerseals.com.